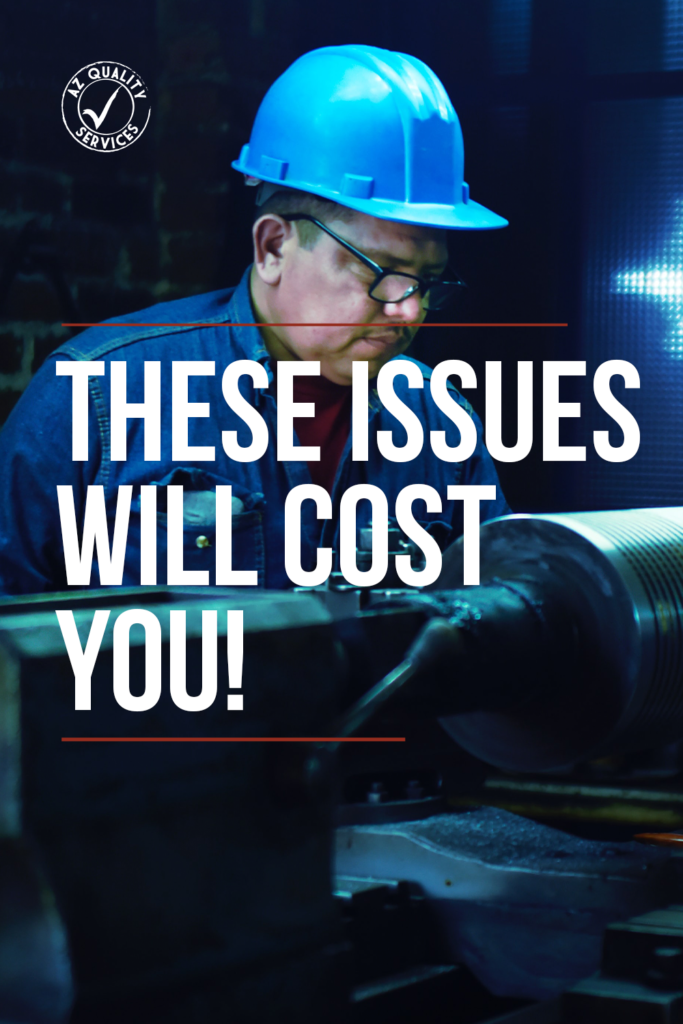
Fix Auto Industry Issues Before They Become Costly Problems
One of the single most dreaded words in any industry is recall. Telling consumers to stop using a product or to bring it in for a repair or refund is not only embarrassing and expensive, but it’s also a brand killer. In this modern age of social media, where a single consumer complaint can be amplified to thousands (or millions!) in minutes, quality is key. Now more than ever it’s critical to address and correct auto industry issues before they become costly problems.
Manufacturing Issues
A typical source of auto industry problems occurs during manufacturing. These issues are often localized and affect individual plants, which makes the problems easier to identify and address.
Typical manufacturing issues include:
- Lack of qualified inspectors (this hit Nissan hard in 2017)
- Substandard materials that go unnoticed, due to lack of quality control
- Supply chain missteps
- Manufacturing defects
- Defective components, such as faulty airbags
Auto Tech Issues
With increased consumer demand for entertainment features and connectivity, automobiles have become technology on wheels. While the addition of high-tech features has increased sales, it has also created more opportunities for missteps. Faulty relays and problems with infotainment units typically aren’t relegated to just one manufacturing plant: they impact most, if not all, of the autos produced. Coupled with the shortage of semiconductors, technological recalls present some of the costliest problems for the auto industry.
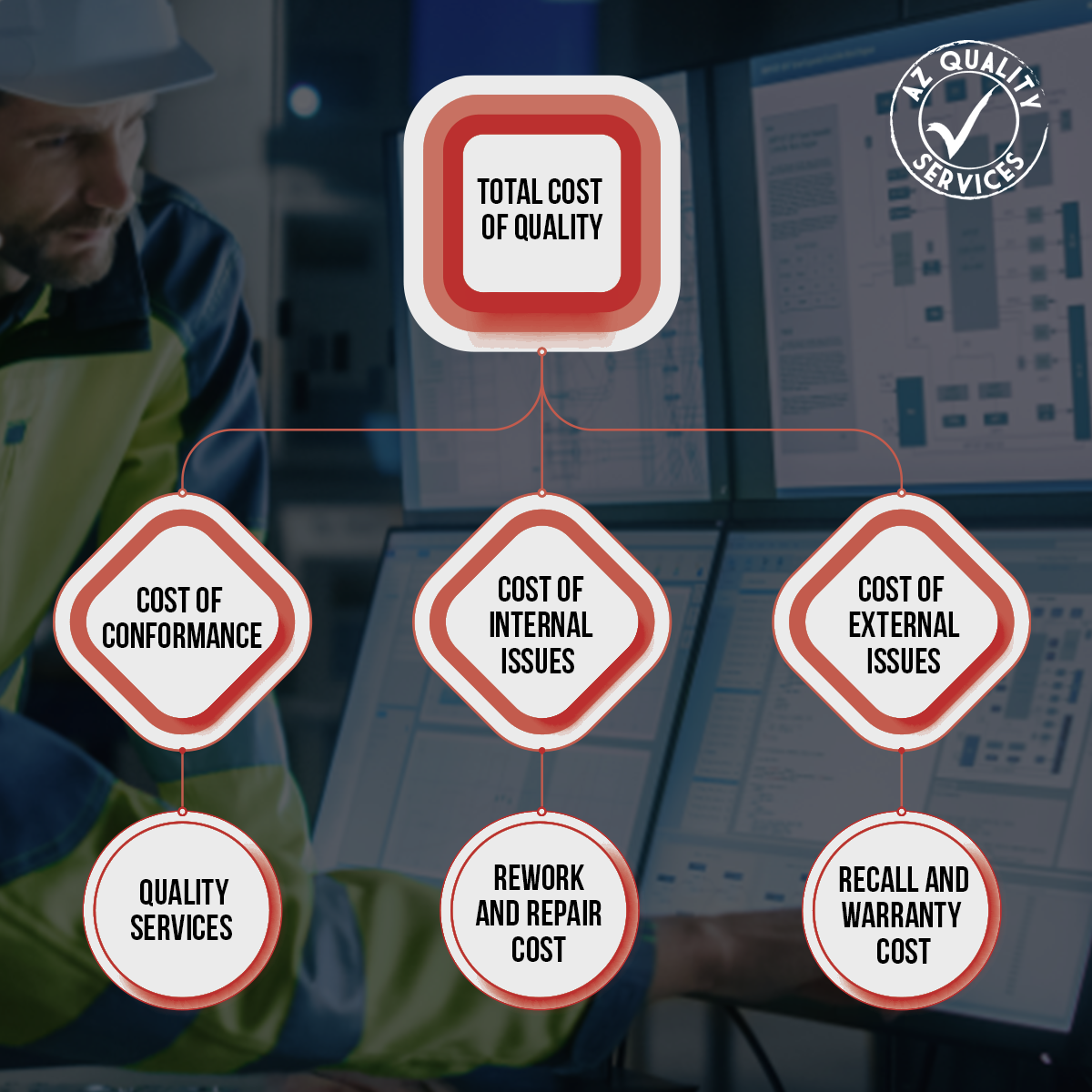
The Cost of Quality
For too long, the auto industry has ignored the rising cost of recalls and essentially accepted it as the cost of doing business. It’s time for a proactive approach. Rather than waiting for problems to arise after the sale to develop a solution, start planning and testing early in the production process to minimize problems altogether. Instead of only budgeting for repair work, recalls, and warranty costs, start investing in quality assessment services. The cost of conformance, or fixing issues before they become big problems, is the most cost-effective option for the auto industry. Quality staff, systems, and resources will minimize the budget needed for non-conformance issues.
We Can Help
AZ Quality Services understands how frustrating it is to deal with unexpected quality issues. We work to protect not just your production schedule, but also your reputation. We have more than 20 years of experience resolving quality issues for our customers and ensuring that their relationships with clients and suppliers are protected. AZ Quality Services offers our customers personalized attention with a solutions-based approach that meets their specific needs. Contact us today to learn how we can help you.
AZ Quality Services management successfully works with manufacturers and service companies supporting a wide range of engineering, technical, mechanical, quality, communications, skilled trades, and other disciplines. We provide a multitude of managed programs and talent-focused contract personnel services supporting complete customer outsourcing needs.