Our Services
We provide these services individually or in tandem based on your process needs.
Our Team is ISO certified, WBE certified, and a proud member of NAWBO.
SERVICES
Visual Inspection
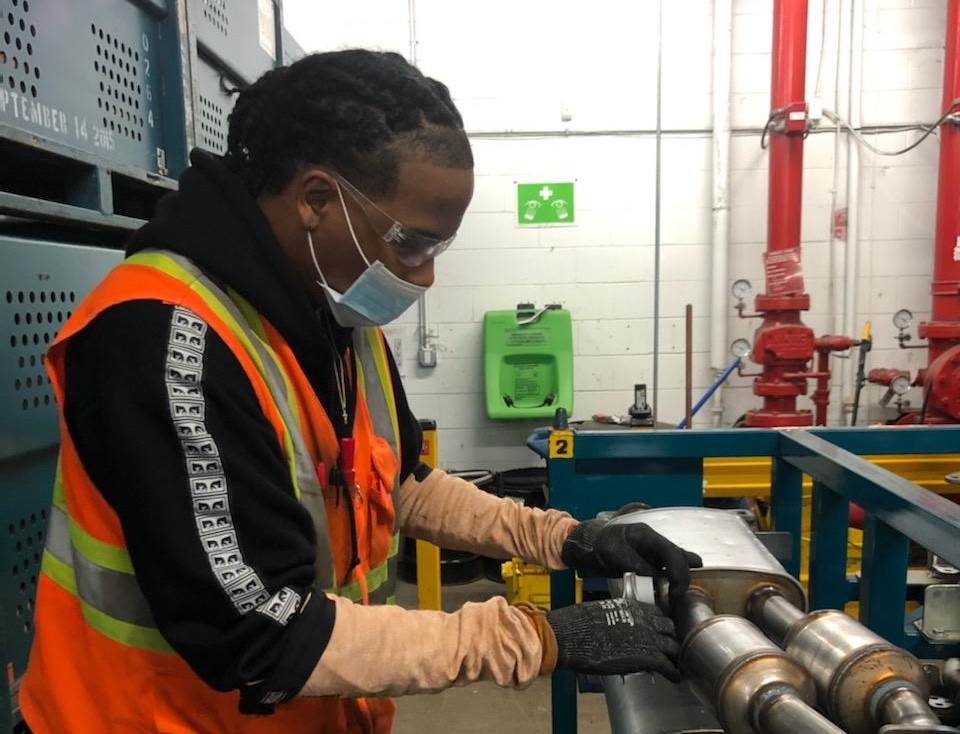
Visually inspect products and ensure company quality criteria is met.
Provide a team responsible for quality assurance, so your employees can focus on the task at hand.
Separate nonconforming from conforming product without additional operations, avoiding rework and repair.
SERVICES
Containment
Identify and remove all defective products and the issues from the manufacturing process.
Remove or recall defective materials from the manufacturing and shipping processes.
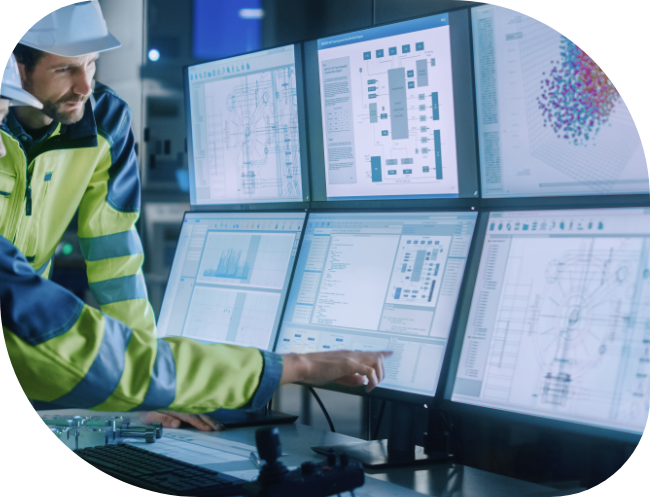
SERVICES
Rework
- Bring nonconforming product into conformance through additional operations that alter the original design of the product.
- Defective products and the issues causing them are identified and remedied within the manufacturer’s process.
- Perform rework tasks, beyond regular processes, to ensure quality is in line with company criteria.
- Get defective products back in spec and eliminate issues at the source until a clean point is reached.
SERVICES
Quality Liaison
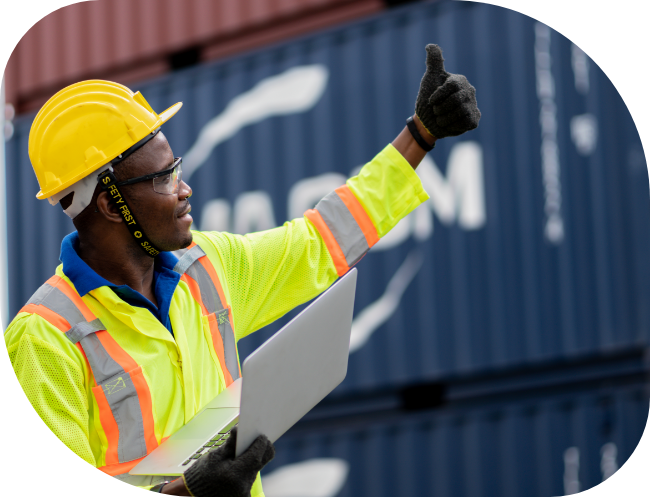
With certifications in CS1 and CS2, we provide a bridge between suppliers and their customers to ensure suppliers are adhering to quality standards.
Ensure products are being installed with the proper care and tools, maintaining and evolving the professional relationship between your organization and your suppliers.
An advocate for product quality, we ensure accountability and improve communication between suppliers and customers to ensure quality standards are met.
SERVICES
Quality Assurance Staffing
Training and hiring the minimum amount of contract employees and staff for the maximum amount of benefit.
Recruit a certified quality inspection team without administering your own internal hiring process.
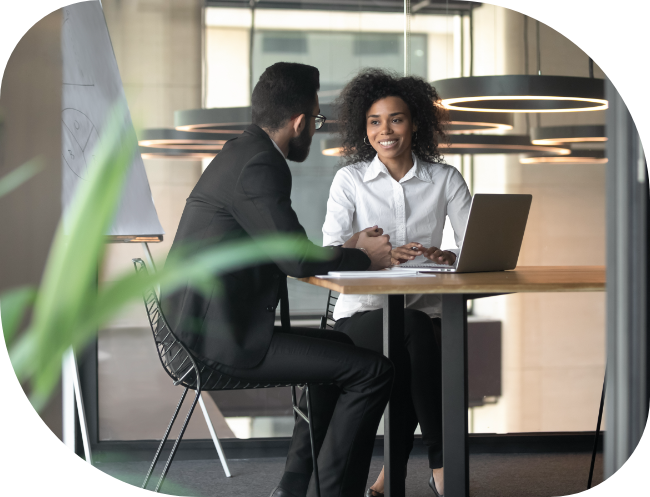
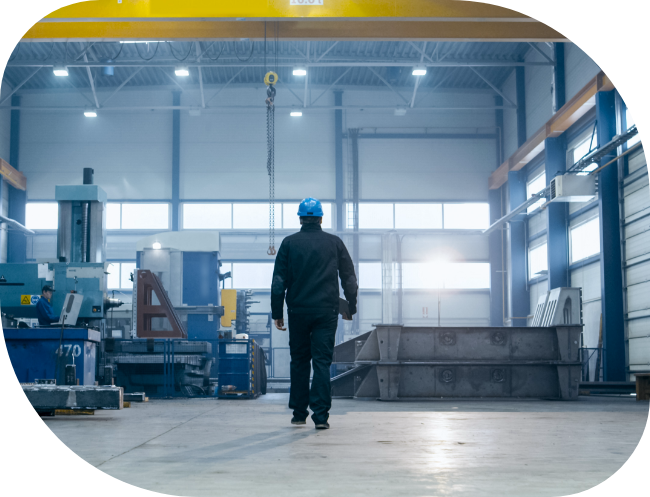
SERVICES
Launch Preparedness
Ensure quality assurance preparedness when launching a new product, providing testing, or training staff on a process.
Proactively manage the quality of products to avoid crisis or line shutdown when debuting products to the public marketplace.
Review new product processes and provide suggestions for more efficient and effective solutions.
Not Sure What You Need?
We’re here to help. Our team is happy to recommend the best services based on your unique needs. Start the process today by booking a free discovery call to receive your quote.
Our Process
You don’t have time to tediously explain your problem and find your
solution. We get it. We make it easy in just five steps.
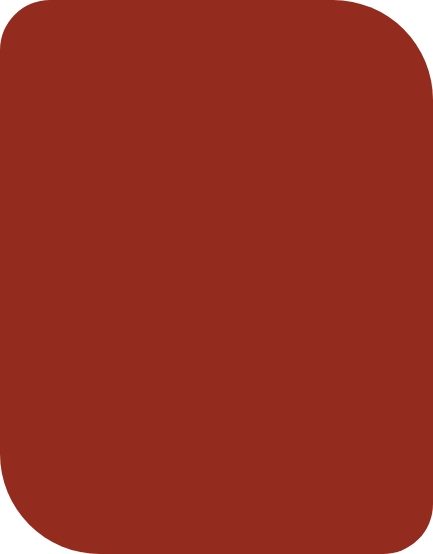
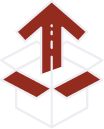
Discovery:
Analyze the problems that you’re facing.
Determine the level of staffing you’ll need.
Rework or contain the issue that your production is facing.
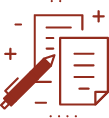
Quality Assurance Assessment:
Collaborate with you about your plant or factory needs to create a transparent support plan (no hidden start-up fees included).
Collect all the information we need to provide you with a quality assurance plan of action.
Recommend staffing needs to resolve the issue(s) currently holding up your line.
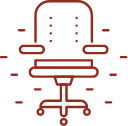
Recruitment & Training:
Assemble a team of ISO-certified inspectors, engineers, and supervisors to quickly solve your issue.
Provide quality assurance team training.
In addition, our teams are trained at your facility to ensure they understand your company’s compliance and safety standards.
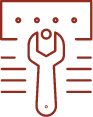
Daily Inspection Reports:
Complete ongoing daily inspection data sheets to ensure your issue is being resolved within the agreed upon standards and established timeline.
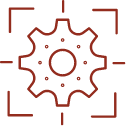
Reach a Clean Point:
Once we reach a clean point, our job here is done!
We continue to be available for future inspections, containment, or rework.
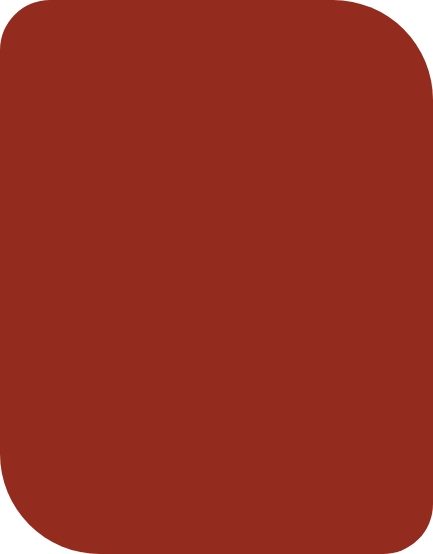
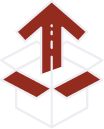
Discovery:
Analyze the problems that you’re facing
Determine the level of staffing you’ll need
Rework or contain the issue that your production is facing.
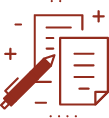
Quality Assurance Assessment:
Collaborate with you and your plant or factory needs to create a transparent support plan (no hidden start-up fees included).
Collect all the information we need to provide you with a quality assurance plan of action.
Recommend staffing needs to resolve the issue(s) currently holding up your line.
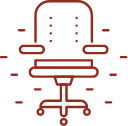
Recruitment & Training:
Assemble a team of ISO-certified inspectors, engineers, and supervisors to quickly solve your issue.
We provide quality assurance training to this team.
In addition, our teams are trained at your facility to ensure they understand your company’s compliance and safety standards.
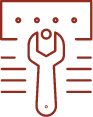
Daily Inspection Data Sheet Reporting:
Complete ongoing daily inspection data sheets to ensure your issue is being resolved within the agreed upon standards and established timeline
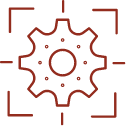
Reach a Clean Point:
Once we reach a clean point, our job here is done!
We continue to be available for future inspections, containment, or rework.